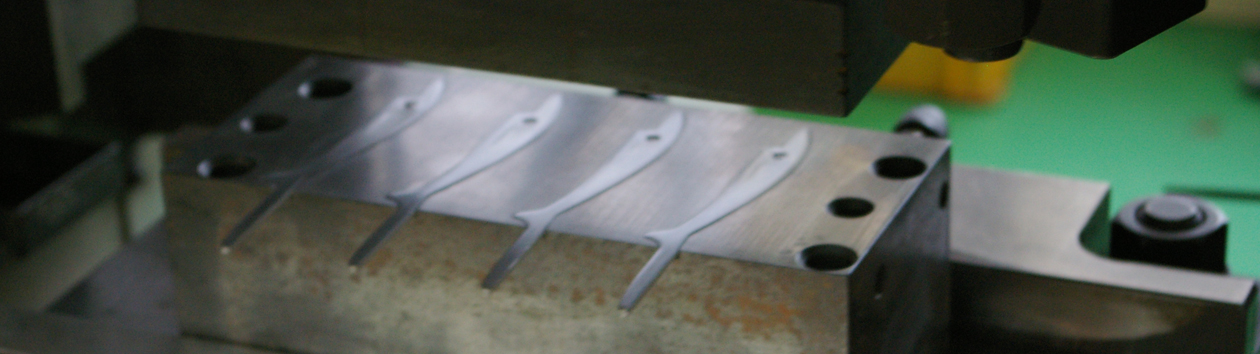
レーザーカッティング
多品種少量生産や複雑な形状に対応できるのはなんといってもレーザー加工です。
プレス切断と違って内部にひずみの原因となる余分な応力を発生させることがありません。
一部の商品はプレス抜きで行っております。
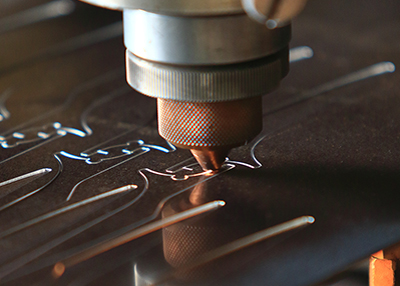
穴開け加工
一本一本熟練工がボール盤での穴あけ加工をしております。
かしめビスの穴やネジビスの穴など商品のグレードによって変えています。
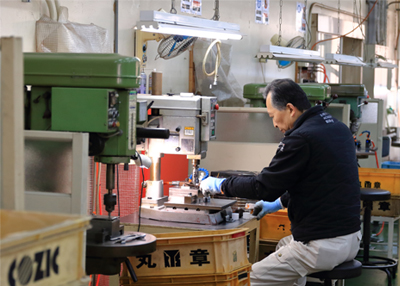
冷間鍛造
R面押し
面押し型という刃材の形状に掘られた型に刃材を置き、450tプレス機により圧力をかけます。これにより、造形はもちろんハサミとしての潜在能力が飛躍的に向上します。
腰段逃がし
面押し型を、さらにハサミの腰にあたる部分の上型を突出させ、450tプレス機で圧力をかける事で刃材に約0.3mmの段差(くぼみ)をつけます。それにより、腰の周動摩擦抵抗が最小になり軽い調子が実現できます。
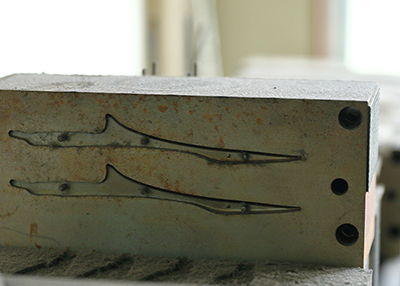
焼き入れ
熱処理加工で、ステンレス鋼を炉の中に入れ加熱・冷却して硬度や性質を変化させて素材の完成度を高めます。
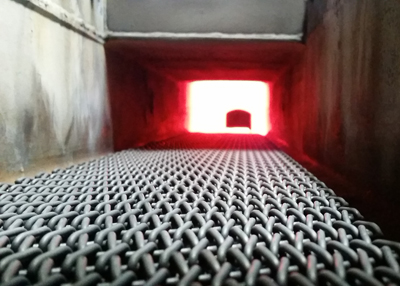
外形仕上げ
背研
刃材の側面がプレス抜き断面になっているため、熟練職人の手によって研ぎ磨きあげられます。
R磨き
鍛造により丸みを帯びたR面を一本ずつ磨きあげることで、きれいな表面と手にやさしい商品が作られます。
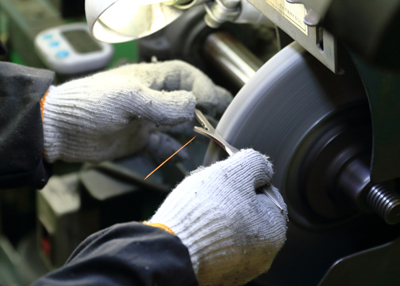
平面バフ
職人による自動バフ機で圧を調整しながら磨き上げます。
表面を磨くことによりキズ・汚れを落とし、表面をきれいにし錆びにくいようにします。
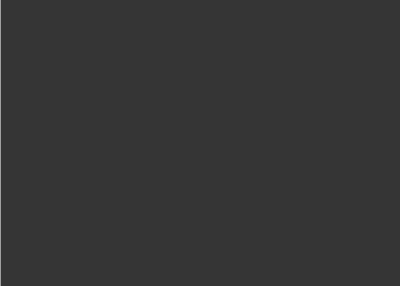
特殊加工
電解研磨
電解研磨液という特殊な酸性の液に沈め、電流を流すことにより表面を磨く(溶解)加工です。それにより、耐食性は向上し表面は光沢がでて美しい仕上げになります。
フッ素コーティング
表面をサンドブラストや洗浄などの工程を経て4フッ化(40%)塗装し焼付けてフッ素コーティングをします。非粘着性、低摩擦性はもちろんの事、その他にも汚れを落とし易く、薬品・熱に強いなど様々な特徴が備わります。
裏
裏刃
はさみを作る上で最も大事な工程であり、用途に合わせた段差を設定する必要があります。主に金属や硬い物を切る鋏には強度上の視点から使われます。
ヒ付け
特殊NC機械を使用し、刃裏をR状にくぼみをつけ用途に合った段差に加工します。構造上内側に巻き込むように切れるため前に逃げることなく確実に切れます。主に繊細な物を切る鋏に使われます。
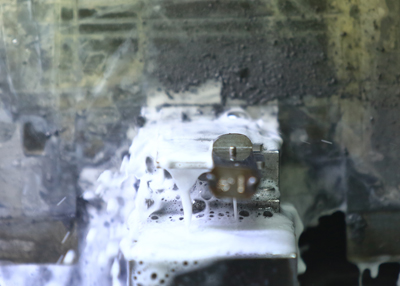
表
表刃
NC機械及び汎用機械により、角度冶具に固定し加工します。商品の用途に応じて角度は設定されます。
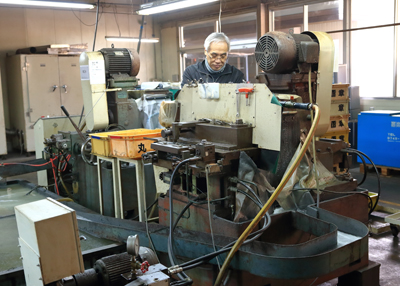
成形
射出成形機で成形型を用いて、ニーズに合った樹脂を使いハンドルを作っています。
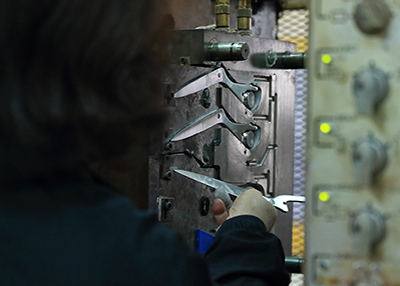
刃付け
NC機械を使用し刃をつけます。細かい砥石、加工の速さを選択し用途に合った加工をします。NC機械の導入により先端の細い鋏の加工が可能になりました。
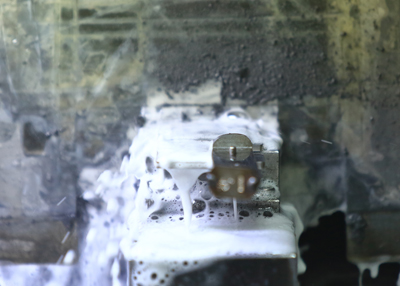
仕組み
ネジ・カシメ・調子出し
組立・検査をする工程で、ネジ・カシメにより組み合わされた鋏が、職人の手によって検査され、鋏の用途に応じた切れ味と調子を出します。
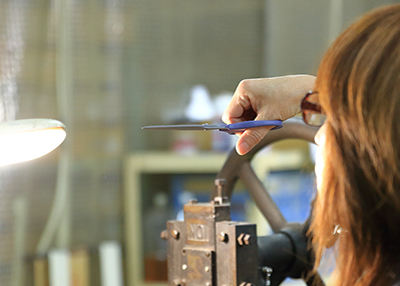
検品・パッケージ
一本一本試し切りを再度行い丁寧に手入れをしてパッケージングします。
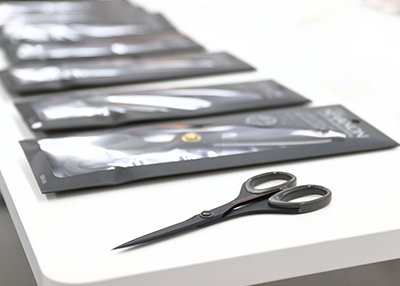